Integrate hardware
A seamless transition from software to hardware testing is critical for automotive software development, bridging the gap between early-stage simulations and real-world validation tests. Working on SDV Platform Validation at NI (now part of Emerson), Matthew Surridge gives us his expert insights.
Integrate hardware
A seamless transition from software to hardware testing is critical for automotive software development, bridging the gap between early-stage simulations and real-world validation tests. Working on SDV Platform Validation at NI (now part of Emerson), Matthew Surridge gives us his expert insights.
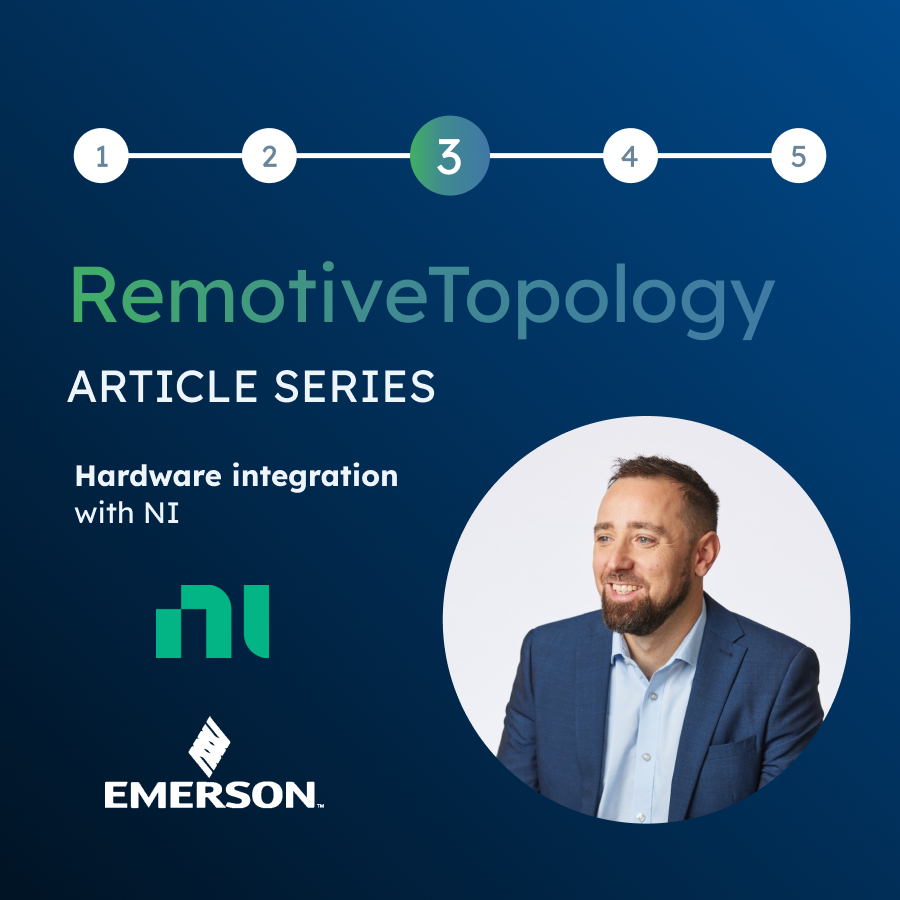
The NI integration
This interview explores how NI and RemotiveLabs collaborate to bridge the gap between software-only (MIL1, SIL2) environments and HIL3 testing. Developing Software Defined Vehicle (SDV) architectures requires a shift in test methodology. There is a need to challenge the traditional hardware testing providers in automotive who are tightly coupled to proprietary ecosystems, limiting integration options and connections to external platforms.
NI holds a significant position in the automotive test and measurement sector, with a modular approach leveraging partnerships as part of its DNA. “Our goal is to be an open test and validation platform where customers can leverage the parts relevant to them. From pure hardware with device drivers as part of a system they build themselves - to us providing a complete software stack with automation tools, asset management, and integrated models” says Matthew Surridge with NI.
The challenge: Painful move from software-only to hardware integration
The goal of software validation is to improve software quality, in order to do it efficiently in automotive there needs to be a more flexible toolchain. Matthew Surridge, SDV Platform validation expert at NI explains: “SIL and HIL providers are generally quite monolithic in their approach, architecture, and offering. When you want to take something out of SIL and bring it over to the HIL world, it won't work. Alternatively, it is very painful to get it running. Because it's so painful, the different teams working on SIL versus HIL just find it easier to start from a blank page which further increases the silos”.
The solution: Enhance realism with the integration of hardware in a software-first workflow
Suppliers team up to meet requirements as the demand for open standards and seamless integration with modern software ecosystems increases. Matthew Surridge notes: “RemotiveLabs and NI easily integrate because they are built on the same principles and mindset around openness.” NI brings a very capable hardware platform into RemotiveTopology: “In a vehicle system built with early MILs or SIL predominantly, you can cover test workflows with integrated hardware by just leveraging the gRCP4 interface to the drivers directly” Surridge clarifies.
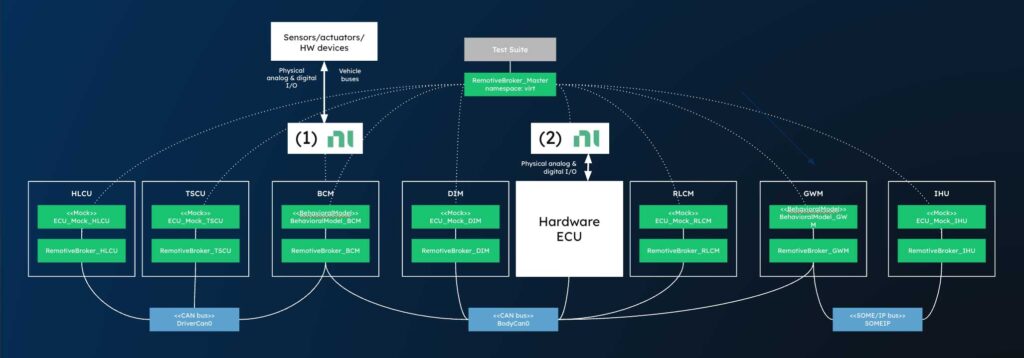
Teams can get going by testing with mocks and models, iterating quickly in SIL environments, and then validating prototype or production ECUs using HIL rigs. By combining open hardware and software ecosystems, teams can reuse test scenarios and reduce silos through full development iterations and ultimately build workflows up to fully automated pipelines, speeding up results as well as gaining and sharing insights across the whole process.
Why RemotiveTopology and NI is a perfect match?
- Modular and open hardware: NI’s platform supports third-party modules and a broad set of I/O capabilities to cover virtually any sensor or signal type.
- Flexible APIs: Leverage NI’s gRPC drivers along with RemotiveLabs gRPC API to connect directly to your existing system or integrate with a complete tech stack.
- Compliance with standards: NI solutions are built to follow industry standards (gRPC, Linux, FMI5/FMU6, ASAM XIL etc.), avoiding proprietary lock-ins.
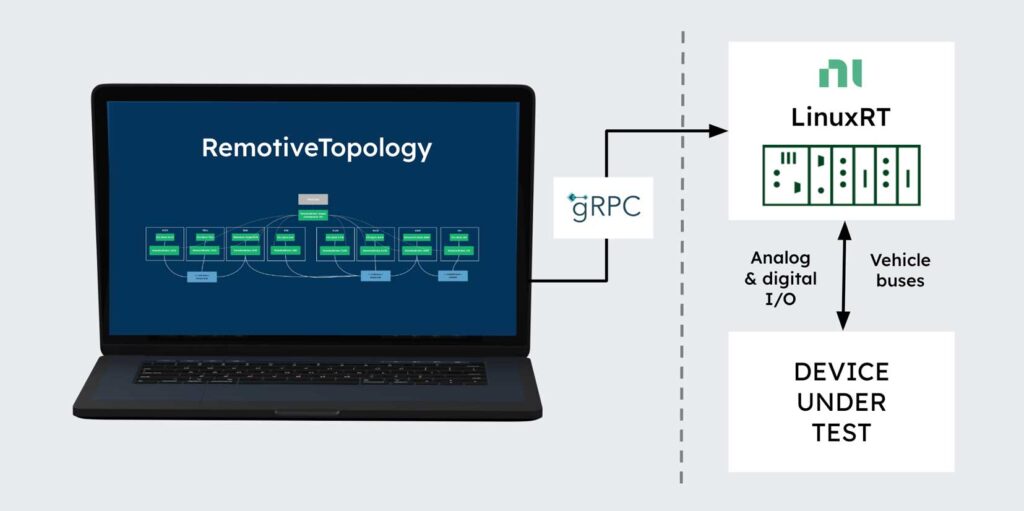
The next-generation hybrid test platforms
The initial integration between RemotiveTopology and NI is just the beginning. Efficient testing demands seamless transitions between virtual and physical environments. A modern toolchain should allow teams to make the journey from 100% virtual testing to full integration of hardware testing with just a few adoptions. “The power and value of tests multiply with a reduced gap from SIL to HIL. The goal is to let teams pick the right mix for their test scenarios without lengthy setups or manual rework,” says Matthiew Surridge with NI.
By embracing open platforms and automation, the next generation of test platforms will significantly enhance asset utilization and team productivity. “To cover for the right test level and relevant scenario, the toolchains for SDVs need to be built on open platforms and technologies with abstraction layers that simplify integrations” concludes Matthew Surridge at NI. NI’s open hardware platform combined with RemotiveTopology offers a vision for demand-driven testing. This integration empowers teams to deliver robust software faster while reducing costs and inefficiencies.
[infobox][center]
Abbreviations in article
1 MIL = Model-in-the-Loop
2 SIL = Software-in-the-Loop
3 HIL = Hardware-in-the-Loop
4 gRPC = Google Remote Procedure Call
5 FMU = Functional Mock-Up Unit
6 FMI = Functional Mock-Up Interface.
[/center][/infobox]
Check out the latest from us
Join the automotive rebels that #getstuffdone with RemotiveLabs!
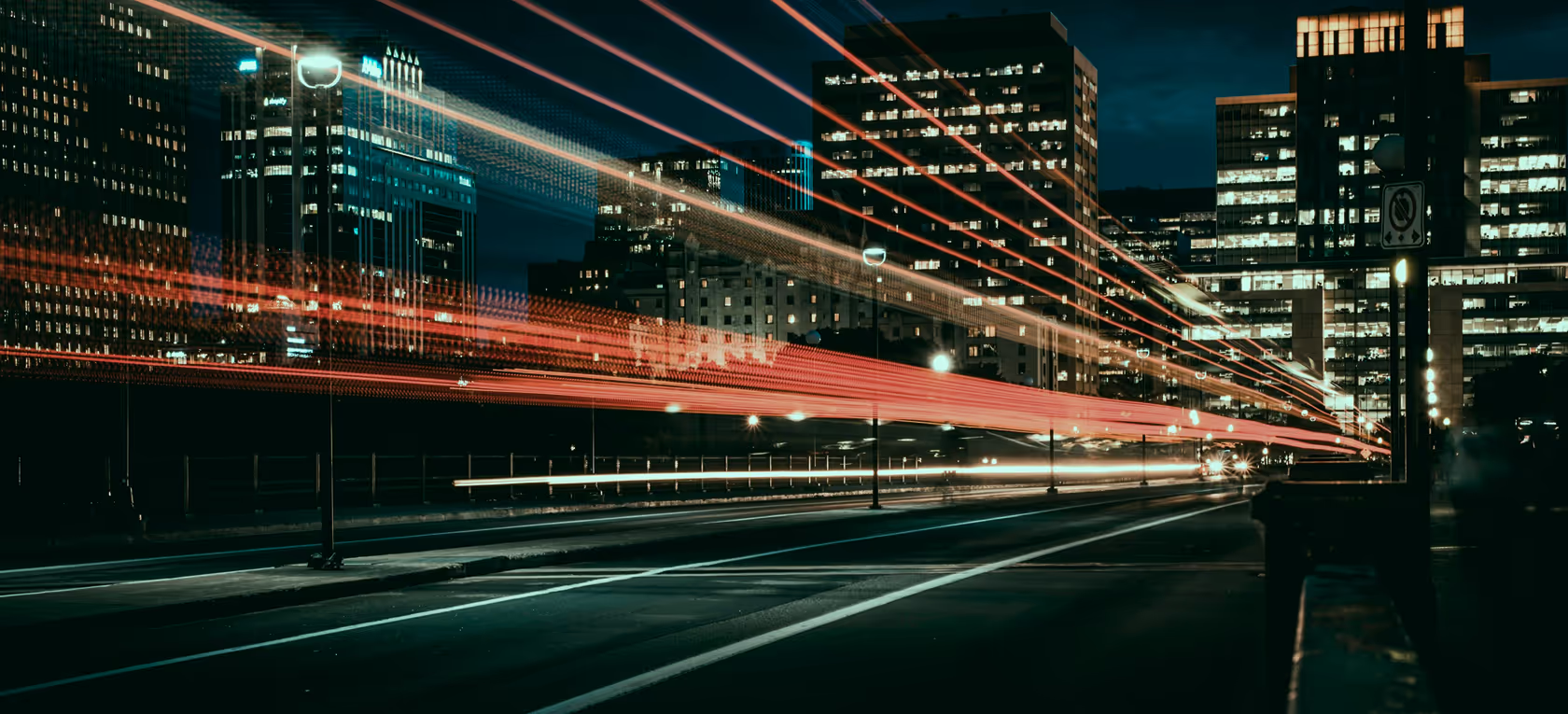